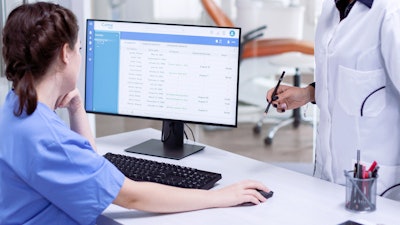
After reviewing thousands of practices, we have found that one of the key factors that keeps production lower than it should be, and significantly below its potential, is how the scheduling system is managed. Practices often have a mentality that if the schedule is busy, you are maximizing productivity.
Unfortunately, any inefficiency can result in lower production. This is true even though you may be working harder and more chaotically, experiencing much higher stress, and potentially burning out your team. At first, this may seem counterintuitive, but mathematical analysis of thousands of practice schedules clearly demonstrates that working more chaotically, which is often interpreted as working harder, creates higher levels of inefficiency rather than improving practice performance.
The physics of scheduling
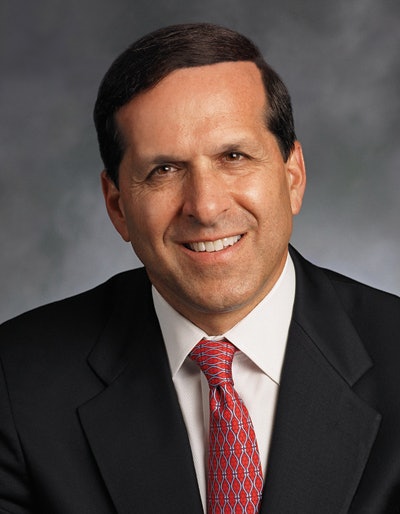
Schedules are based on time, and time is finite. There are only so many ways to maximize production in an eight-hour day.
But there are ways, and those ways need to be understood by every practice. All lost production adds years to reaching financial independence. Here are steps you can begin to take to improve your schedule by 30% or more in terms of capacity.
1. Set annual production goals. Schedules should be based on setting an annual production goal. If your practice does not have an exact production goal every year, you are making a fundamental mistake.
Many schedules are built in such a way that the practice cannot exceed a certain level of production and will not. We receive regular contact from practices that are frustrated that their production has not risen or risen to the level that they would expect.
After analyzing their schedules, we often find that the current schedule is the barrier, and capacity simply will not allow for growth. This is often compounded by how patients are put into the schedule for varying procedures.
Action: Set an annual production goal prior to making any scheduling changes.
2. Establish a rigorous daily production goal. Once the annual production goal is set, it should then get broken down into a daily goal. But as we have found in advanced scheduling management, not all days are equal.
For example, in some practices, Thursdays are much heavier treatment days with much higher production. Yet, we continually find all types of procedures shoved into Thursdays, when the practice should be focused almost exclusively on larger cases.
Not only does this create much higher stress, but it decreases overall production, as the number of higher production cases that can be scheduled and completed is more limited. And this is merely one example.
The front desk team needs to be trained that their No. 1 objective is to build the schedule to hit the daily production goal. They must understand the protocols, deliver five-star customer service, and not continually make exceptions.
Unfortunately, many practices confuse giving five-star service with giving patients anything they want, which disrupts systems and lowers production. However, it is possible to achieve five-star customer service while following preset scheduling protocols.
Action: Instruct the front desk scheduling team that their main objective is to be within 10% of the daily production goal in over 90% of the days.
3. Understand the fluctuations in patient flow in your practice. Consider the following questions:
- Is there a specific day of the week that is more desired by patients for higher-production procedures?
- Are there times of the year when the practice is busier than other times?
- Are there more desirable appointment times for patients, such as mornings or afternoons?
- Does the front desk scheduling staff have protocols for handling emergencies?
- What does an ideal day look like for each day of the week?
- What does an ideal month look like for each month of the year?
The key is then to build the schedule around variation. While it may seem simpler to schedule every day the same way, it also lowers production.
We have seen tremendous success by scheduling production goals differently for certain days and different months based on the ability and capacity of the practice. We have also seen practices that have added hours during certain seasonal busy times and decreased hours during lower-demand times. Ultimately, this will increase production by 30% to 50% within about three years.
Action: Build your schedule based on the best opportunities. Schedule only specific procedures based on production for days that have the most opportunity and shift lower-production procedures to other days.
4. Block the schedule. Train the team to block the schedule based on procedures. We see many practices that have high-volume days, low-volume days, and days that are all over the place. It's exhausting. Once again, smaller procedures that are lower production can crowd out the opportunity to schedule larger procedures.
The key is to block out specific times for the specific length and production levels of high-production procedures. This is the only way that most practices will be able to control the production flow.
One reason this has not occurred is that the last 10 years prior to the pandemic were excellent regarding practice production and the economy. As that is changing, some practices are finding that their production has been reduced and they need new strategies and methods to increase production.
You must find the right solution if the practice is struggling to fit patients in. As one scheduling policy example, one of our most powerful production scheduling recommendations is that all new patients should be seen within seven to 10 days.
New patients have two to three times the financial value of a current active patient in the first 12 months. If the schedule cannot accommodate that, then overall production at year-end will be lower.
These are a few of the key elements of building a schedule. Others, such as rigorously following excellent scripting, can make a tremendous difference in how patients cooperate with scheduling protocols. For example, how should your practice handle a patient who wants to have their follow-up check on a Monday if the protocol doesn't allow for this? With proper scripting, this patient can still receive care and compassion, excellent customer service, and a convenient appointment time for another day.
Using blocks to ensure the right production and understanding how to vary production by day or by month are also key factors for practices based in specific regions, such as the south having the "snowbird effect."
Overall, we have seen practices increase production 10% to 30% or more by building a schedule that allows for better integration of appointments, maintaining production blocks, and understanding overall patient flow. Remember, it should all be mathematically based. There are also additional factors, such as new patients, which can often comprise a significant percentage of practice production for many surgical practices and how they are managed versus multiple appointment cases and follow-up checks.
Summary
Scheduling is the command-and-control system that helps manage all other practice systems. If you get the scheduling system right, other systems can be built to excellence. If you get it wrong, other systems can only reach certain levels of maximum potential regardless of how well they are designed. Take the time to analyze the schedule mathematically and then build an ideal schedule that will not only increase production but lower stress and fatigue.
Dr. Roger P. Levin is CEO of Levin Group, a leading practice management and marketing consulting firm. To contact him or to join the 40,000 dental professionals who receive his Practice Production Tip of the Day, visit LevinGroup.com or email [email protected].
The comments and observations expressed herein do not necessarily reflect the opinions of DrBicuspid.com, nor should they be construed as an endorsement or admonishment of any particular idea, vendor, or organization.