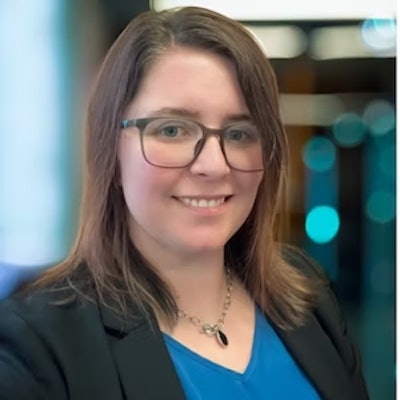
Editor’s note: This is the fifth in a series of articles in which we will bring in an expert to address some of the misinformation we have read in various social media posts and groups. You can see some of the previous installments at the bottom of this article.
Q: In school, we talked about using hospital-grade disinfectants for clinical cleaning and disinfection. Now I can’t find anything about hospital-grade disinfectants. Where do I look?
A: Ensuring that your facility uses the correct product for cleaning and disinfection can be a tricky job. The term “hospital grade” is a slang term for disinfectants that are used in hospitals, but there are many different types of disinfectants that fall into this category. Let’s start with the basics.
Initially disinfectants can be divided into the following three categories:
- Low-level disinfectants kill most bacteria and fungi and inactivate some viruses, but they do not kill Mycobacterium tuberculosis.
- Intermediate-level disinfectants kill most bacteria, including M. tuberculosis and all fungi, and they inactivate most viruses.
- High-level disinfectants -- also known as “cold sterile” in the dental community -- kill bacteria and fungi and inactivate viruses very effectively. They do not, however, kill high levels of bacterial spores. These chemicals can be considered chemical sterilants when the contact time is increased to a longer period of time (six to 10 hours).
Within these three categories, different chemical compounds are used against different microorganisms.
- Low-level disinfectants include quaternary ammonium compounds, or quats; phenolic compounds; and iodophors.
- Intermediate-level disinfectants include alcohols, chlorines, and oxidizing agents.
- High-level disinfectants include aldehydes and oxidizing agents. These chemicals are harsh and tend to be very dangerous for staff. They may also require extensive monitoring procedures. There are multiple alternatives to cold sterilants, including moving away from an aldehyde chemical or moving to equipment that can be heat sterilized. If you’re still using cold sterile in your office, work with your product rep to find a safer alternative.
Many disinfectants on the market will mix and match chemicals to create an effective low or intermediate solution. One very common brand of disinfectant used in dentistry is a mix of alcohol and quat compounds to create an effective intermediate-level disinfectant.
There are also newer combinations of chemicals coming out that are hydrogen peroxide-based that boast a reduced contact time and are not as harsh on equipment. These are also important points to consider when choosing a disinfectant.
To decide which disinfectant your facility needs, it’s important to do a risk assessment of the different microorganisms your staff could be exposed to. For clinical contact surfaces, consider an intermediate-level disinfectant that is approved to kill at least M. tuberculosis. You can also include other microorganisms in your search, like hepatitis B, HIV, and even SARS-CoV-2.
Once you have decided on what you want to kill, you can search for appropriate disinfectants on the EPA’s website. The lists include all disinfectants that have a claim to kill microorganisms, and many of them include more than what would be needed in a dental facility. For example, if your facility has decided you need a disinfectant that will work on M. tuberculosis, hepatitis B, and HIV, you would look on the EPA’s List E for products that have been validated to kill those three microorganisms.
This resource is great to search if you’re looking for a new disinfectant to add to your facility, but what if you want to verify if what you’re already using is effective? You can start simply by reading the product label.
Registered disinfectants are required to include the EPA registration number, active ingredients, what microorganisms they kill (in addition to the contact time for each), first aid instructions, use instructions, cautionary or warning language, and storage and disposal instructions. If you want to check your current disinfectants on the EPA website, you can do so by entering the information you find on their search platform. Some disinfectants are repackaged under a different name, so you might not find the name of your disinfectant on a list. If this happens, search by the EPA number.
Here are a few other tips when it comes to disinfectant use in your facility:
- In addition to finding out which disinfectants will work best in your facility, it’s important that your staff is trained to use them properly. Many solutions will include different contact times on the label based on the microorganisms you’re trying to kill. Including training for all staff ensures consistency in processes and helps reduce confusion.
- Reducing the number of different disinfectants in your facility also reduces confusion with staff. If a facility has four different chemicals, all with different instructions for use, it’s only a matter of time before something is used incorrectly. Simplifying the number of disinfectants in your office also removes the chance of mixing chemicals unintentionally, which can turn into a dangerous situation very quickly.
- Don’t forget that a disinfectant won’t disinfect if there is a bioburden that remains on the surface. Every surface should be precleaned to remove the bioburden before the disinfection process occurs. Most disinfectants available are also approved as cleaners, so double-check whether using the same chemical for both processes is indicated by the instructions for use. Staff will want to ensure the surface is clean first with one wipe and then wipe a second time to apply the disinfectant, which needs to remain visibly wet for the entire recommended contact time.
- Ensure you allow enough time for the cleaning and disinfection process to happen. If the disinfectant doesn’t remain wet for the entire recommended contact time or staff are setting up the operatory before the disinfectant is dry, it’s not doing its job, and you have the potential for cross contamination from patient to patient.
Choosing and using disinfectants is a more complicated process than most are aware of, but they are critical to keep your patients safe. Take these tips back to your staff at your next huddle to make sure your office is operating at the gold standard of disinfection!
References
- Disinfectants are Characterized into 3 Activity Levels. Oakland University. Retrieved from https://www.oakland.edu/Assets/upload/docs/LabSafety/disinfectantsFinaLAug2009.pdf. Published 2024.
- How to Read a Disinfectant Label Infographic. Retrieved from https://www.cdc.gov/hai/pdfs/howtoreadalabel-infographic-508.pdf. Centers For Disease Control and Prevention. Published 2024.
Sarah Stream, MPH, CDA, is a seasoned dental professional, educator, and speaker. She is passionate about being a lifelong learner and sharing knowledge with other dental professionals on a safe dental visit and compliance. She currently specializes in OSHA, HIPAA, and infection control, supporting dental facilities with their education and compliance needs. You can contact her at Stream Education and Consulting LLC or via email at stream.education.and.consulting@gmail.com.
The comments and observations expressed herein do not necessarily reflect the opinions of DrBicuspid.com, nor should they be construed as an endorsement or admonishment of any particular idea, vendor, or organization.