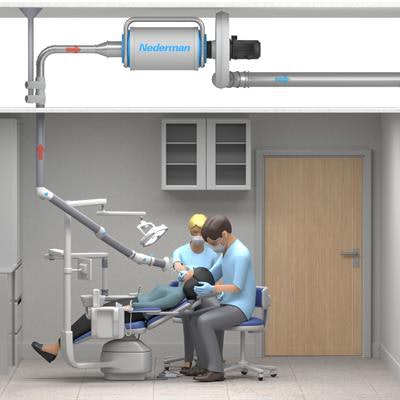
Wearing personal protective equipment (PPE), sending sick employees home, and integrating indoor air quality control strategies, such as air cleaning, can reduce exposure to SARS-CoV-2. However, installing extraction arms can take safety to the next level at dental offices.
Aerosol extractors, such as Nederman FX2 extraction arms, capture droplets that may contain disease-causing pathogens as close to the source as possible, removing them before they reach the breathing zones of patients and dental teams and spread throughout the office.
"Engineering controls, like the arm, isolate people from the hazard," said Phil Templeton, vice president of sales at clean air equipment provider Nederman.
"With this in place, you know you did the best you could to protect dentists, hygienists, and patients."
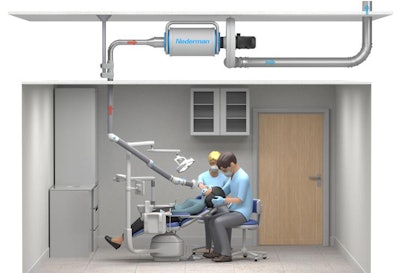
Trying it all
Airborne transmission, likely from asymptomatic individuals with SARS-CoV-2, is believed to be the way the novel coronavirus became so widespread, killing an estimated 170,000 people in the U.S. Because they work closely with patients in tight quarters, dental practices need to do whatever they can to minimize the risk of contracting the virus via aerosols, which are produced when people breathe and talk.
As scientists work on vaccines and therapies for COVID-19, the respiratory disease caused by SARS-CoV-2, dental practices have incorporated telehealth, starting taking patients' temperatures, and asked patients to wait in their cars to allow for social distancing, as well as other infection control measures. Scientists have encouraged dental offices and other facilities to integrate indoor air quality control measures, such as using standalone air purification equipment and making ventilation changes. One dentist in Oregon went a step further by turning her office into a clean room, which included the installation of Nederman arm. But what is this method and how can it benefit dental teams and patients?
From old to new
Source capture methods have been used for years to collect fumes, dust, and gases in labs and research settings; diesel exhaust from first responder vehicles; industrial dust at manufacturing plants; and oil mist and smoke at metal machining plants. When the pandemic struck and dental teams were labeled some of the most at risk for virus exposure, Templeton said source capture made perfect sense as a safety measure. In fact, dentists from Italy and Spain, where the pandemic struck hardest first, began inquiring about equipment that could help with aerosols.
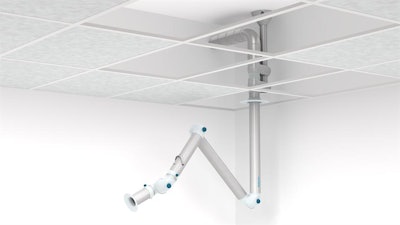
Next-level protection
The use of PPE is the least effective way to protect people from aerosol-generating procedures, according to the National Institute for Occupational Safety and Heath's (NIOSH) Hierarchy of Controls. Administrative controls are a bit better, but NIOSH and the Occupational Safety and Health Administration (OSHA) favor engineering controls. They aim to remove a hazard at the source before it has any contact with a patient or worker.
Air cleaning includes air filtration with high-efficiency filters and adequate airflow within buildings and rooms. Using high-efficiency particulate air (HEPA) filters in recirculated or mixed air ducts can limit cross-contamination among rooms and boost the delivery rate of clean air to weaken the virus concentration in buildings. An extraction arm goes a step further.
"Think of it like secondhand smoking," he said. "It can be blown in the other direction, but some contaminants are still going by people. The arm captures the aerosols before it reaches the air stream."
A 3-inch extraction arm sits 6 inches to 12 inches, ideally at a 45° angle, from a patient, and a fan sucks up the aerosols. They are taken away from the breathing area and exhausted through the ceiling. Depending on practice layout and existing systems, the aerosols can be safely exhausted outdoors or recirculated via HEPA-filtered air.
"It captures 97% to 100% of contaminants," Templeton said.
More protection, more money
Engineering controls can be more expensive than maintaining a supply of PPE or taking administrative actions, but in the long-term, operating costs are often reduced and the level of protection is greater.
Many variables factor into pricing. The cost of the equipment can range from $1,300 to $2,000 per chair, excluding the cost of installation.
Nederman has partnered with Benco to distribute the products, which are in stock. About a dozen offices have had the equipment installed, and many practices across the U.S. have requested estimates, he said.
Knowing what's available
More inquiries are expected as more people learn about the equipment, he said.
"People are getting to know about source capture," Templeton said. "Dentists need to know what they are looking at and what options are best. They have so many things being thrown at them now, and they can't assume everything is equal."